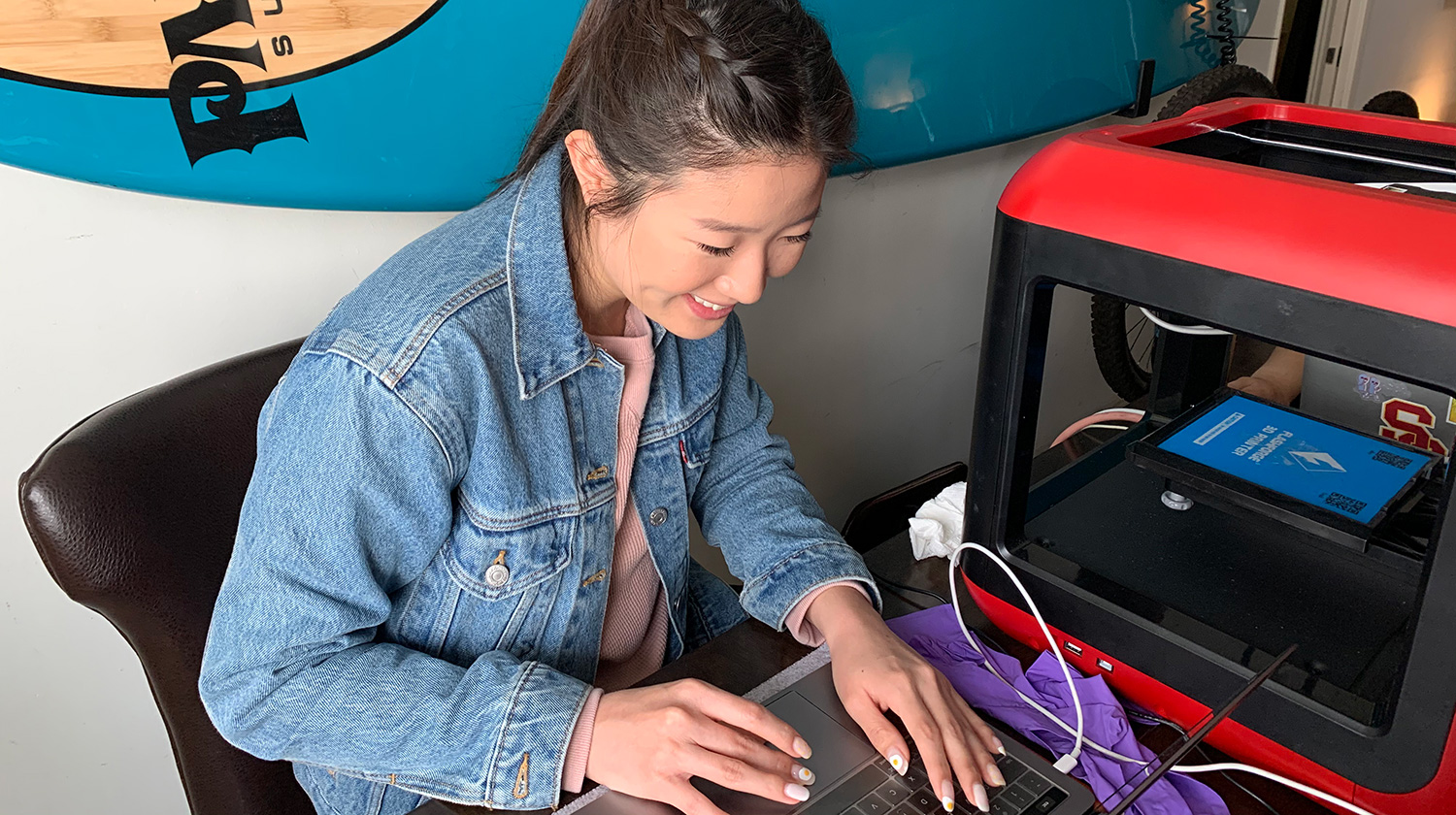
Heeding the call of health care professionals, two faculty-led groups at California State University, Dominguez Hills (CSUDH) are using 3D printing to help supply local hospitals with the face shields they need to reduce the risk of infection on the frontlines of the pandemic.
Taking on the challenge are Paul Penoliar, lecturer and clinical instructor in the Master of Science in Occupational Therapy (OT) Department, and Kamal Hamdan, Annenberg-endowed professor and director of the Center for Innovation in STEM Education (CISE) at CSUDH.
Resourceful and Nimble
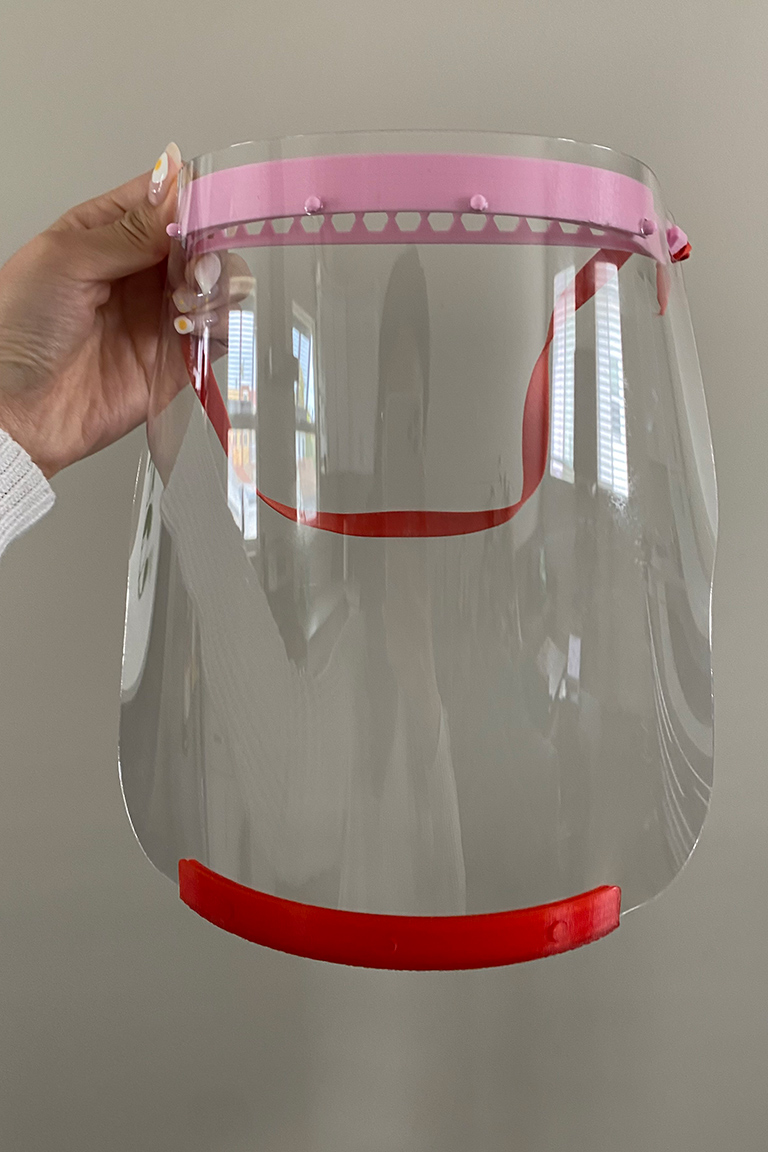
In mid-March, CSUDH converted all in-person instruction to online classes to help prevent the spread of COVID-19. This compelled Penoliar to solicit the help of two of his OT students, Elvy Fuentes and Deborah Han, to move his department’s four new 3D printers to his home in Glendale to manufacture face shields.
To create the designs, the students downloaded a free file from Prusa Research. “3D printing is new to us, but we quickly jumped into the fight to help, while adhering to infection control protocols within the confines of my home,” said Penoliar. “We started fiddling around with the printers and figured it out. My computer-savvy students modified the designs to make the parts, and we were off.”
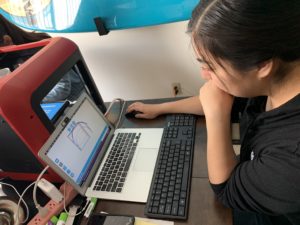
The following day, Penoliar began laser cutting parts for the shields at his home. He ran the printers for 12 hours a day for more than a week to produce the smaller components of the face shields, while also conducting online lectures for his students and preparing for midterm exams.
Polyethylene terephthalate glycol (PETG), the clear material needed to produce high-quality protective shielding, is currently in short supply. Penoliar’s students began cold-calling dozens of vendors and were fortunate enough to find the supply they needed to laser cut the main clear part of the shields.
To get assistance cutting the large sheets of PETG, the students reached out to Glen Morgan, owner and managing director of Studio eQ in Hermosa Beach, who generously cut all 200 shields for free.
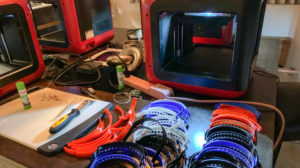
“There were a lot of obstacles, and we didn’t know what to expect. We had to learn to problem solve together. We divided and conquered and figured out how to use the laser cutters for the small parts,” said Han. “We did need some help with the clear face shields, so we reached out to different companies that were trying to do the same thing, and found Glen. He was also printing shields, but didn’t know which hospital to send them to. So we became each other’s missing link. It is a wonderful example of people coming together in uncertain times.”
Han said they have already distributed shields to Glendale Adventist Medical Center. More will go to Long Beach Memorial Medical Center, and to CSUDH faculty who may need them at the hospitals where they work.
Innovation Experts
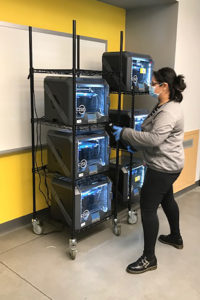
CISE brings science, technology, engineering, and mathematics (STEM) education – including 3D printing – directly to middle and high schools in the region through its fabrication laboratory (fab lab) programs.
Daily Breeze: Attention, hospitals: CSU Dominguez Hills students have created 1,500 face shields to protect against coronavirus
Hamdan knew he couldn’t let CISE’s nearly 400 3D printers sit idle during the pandemic. He set up a Zoom call with staff and undergraduate STEM students to brainstorm ways to repurpose the fab lab equipment.
“I said let’s find a way to print face shields,” Hamdan said. “Our team is amazing. Within half an hour the right file was located online, the software was identified and downloaded, and others began trying to locate materials to purchase. We soon had three protypes of the face shields.”
Hamdan ran into the same problem as Penoliar’s team – a lack of PETG to buy and print the clear part of the shields. CISE purchased transparencies instead.
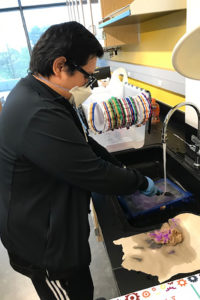
“We drove to many office supply stores to buy transparencies, and we were fortunate to find enough to start production,” he said. “We were poised and ready to help.”
CISE is using approximately 50 of its larger 3D printers to print the face shields. They set up an assembly line to program the printer, run the laser cutters, and assemble the parts. Production is taking place in the Toyota Center for Innovation and STEM Education, located in CSUDH’s new Science and Innovation Building.
Their initial attempt to cut a shield took nearly three hours. The team has reduced that to 27 minutes, with the potential to produce 100 face shields per hour. CISE is now exploring adding filtered facemasks to its production.
“We have the most amazing team, and our STEM students are just brilliant and so driven. Both dropped everything and began working day and night trying to figure out how to get this done,” Hamdan said. “These are forward thinking, decent people, who are so motivated to make a difference in others’ lives. I am so proud of them all.”